Electric drive technology
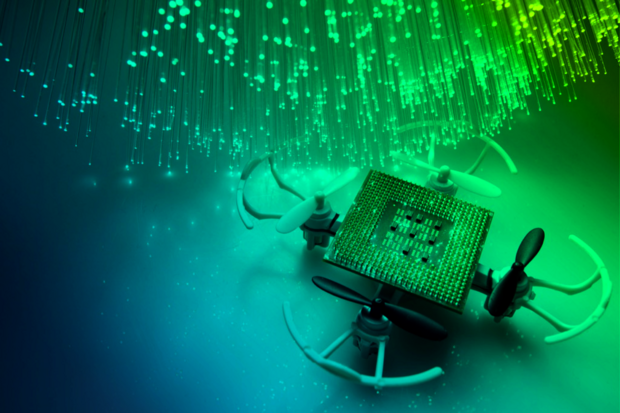
Contact person: Prof. Dr. Matthias Förster
Contact details:
Tel.: +49 3641 205 717
E-Mail: matthias.foerster@eah-jena.de
Web: Homepage
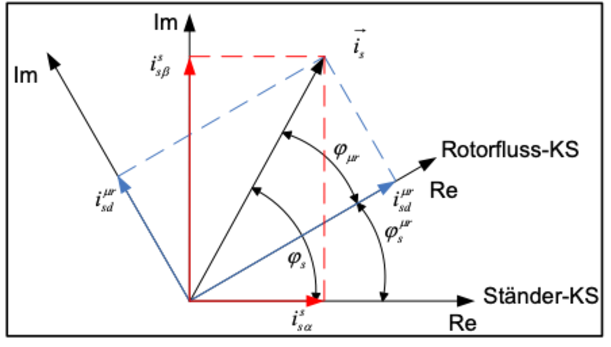
Efficient control of position and speed of electric machines is a primary goal in industrial applications. Field-oriented control meets these requirements. The rotor flux position is required for this control, which can be determined either by using a sensor signal or through mathematical models of the machine. With models, the machine can be controlled without a sensor, and the position sensor can be eliminated. This determination must function across the entire speed range, from standstill to high frequencies. There are different models for different speed ranges. For many industrial applications, sensorless control would be recommended.
If you need assistance with implementation or are interested in solutions, simply contact us.
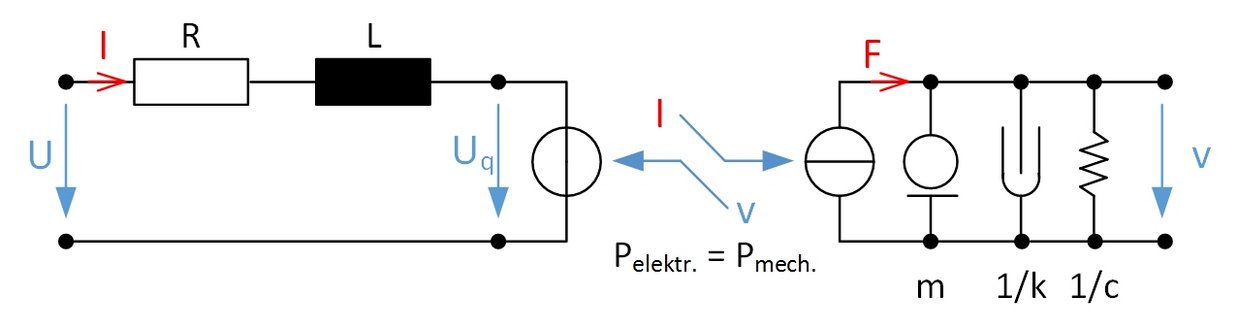
The control of actuators is a complex structure that can consist of multiple control loops. Various physical parameters (e.g. inductance, time constants, moments of inertia, etc.) are required to control the current, speed, and position of actuators. These parameters affect the electrical, magnetic, and mechanical systems. There are different methods to determine these parameters in standstill as well as during operation. Parameter adaptation is also possible.
If you still need a parameter or have questions, feel free to contact us.
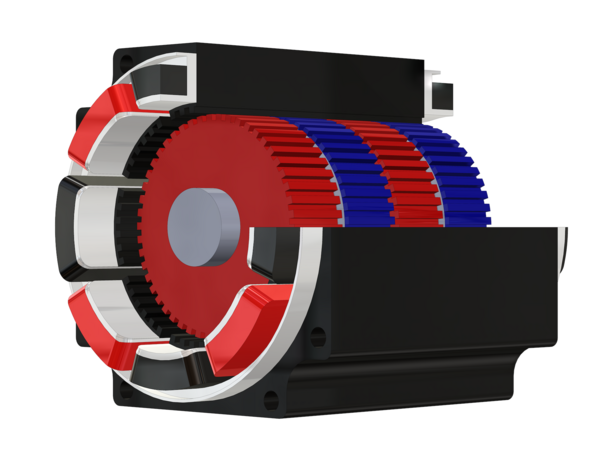
In order to make the development of new actuators and the revision of existing ones more efficient, as well as to gain understanding of current actuators, simulation tools are very helpful. The design and behavior of the magnetic circuit as well as the temperature or control behavior can be represented, adapted, and optimized with these tools. We use the simulation tools Maxwell Ansys and Matlab Simulink. By using DSPACE systems, a prototype commissioning can be carried out quickly.
If you want to adjust, commission and understand actuators, just contact me.